After several iterations with code and experiments with body positions, here’s the final version of the Quadropod for your judgement. Controlled over Bluetooth with a general purpose controller Android app.
Let me know what you think.
After several iterations with code and experiments with body positions, here’s the final version of the Quadropod for your judgement. Controlled over Bluetooth with a general purpose controller Android app.
Let me know what you think.
Today I focused on several things:
Rework of the code is complete. Now it’s completely based on the timer interrupt. I must admit, it’s a huge difference in the way motion feels and is programmed. The level of control over what happens and when is tremendous. Exciting!
After a bit of experimentation I finally figured that working with servos from the main program loop is not very efficient and precise. The main issue I’ve been facing is synchronous and controlled rotation of several servos to different angles.
Short recording of the first baby steps. Woo hoo!
Parts printing and assembly has finished. After initial calibration, I’m now writing simple scripts to see the limits of the platform. We started with push ups:
With that done I’ve looked into how to lift the leg without tipping over. It took a bit of time to figure out the angles of the rest of the legs so that the center of mass shifted backwards slightly.
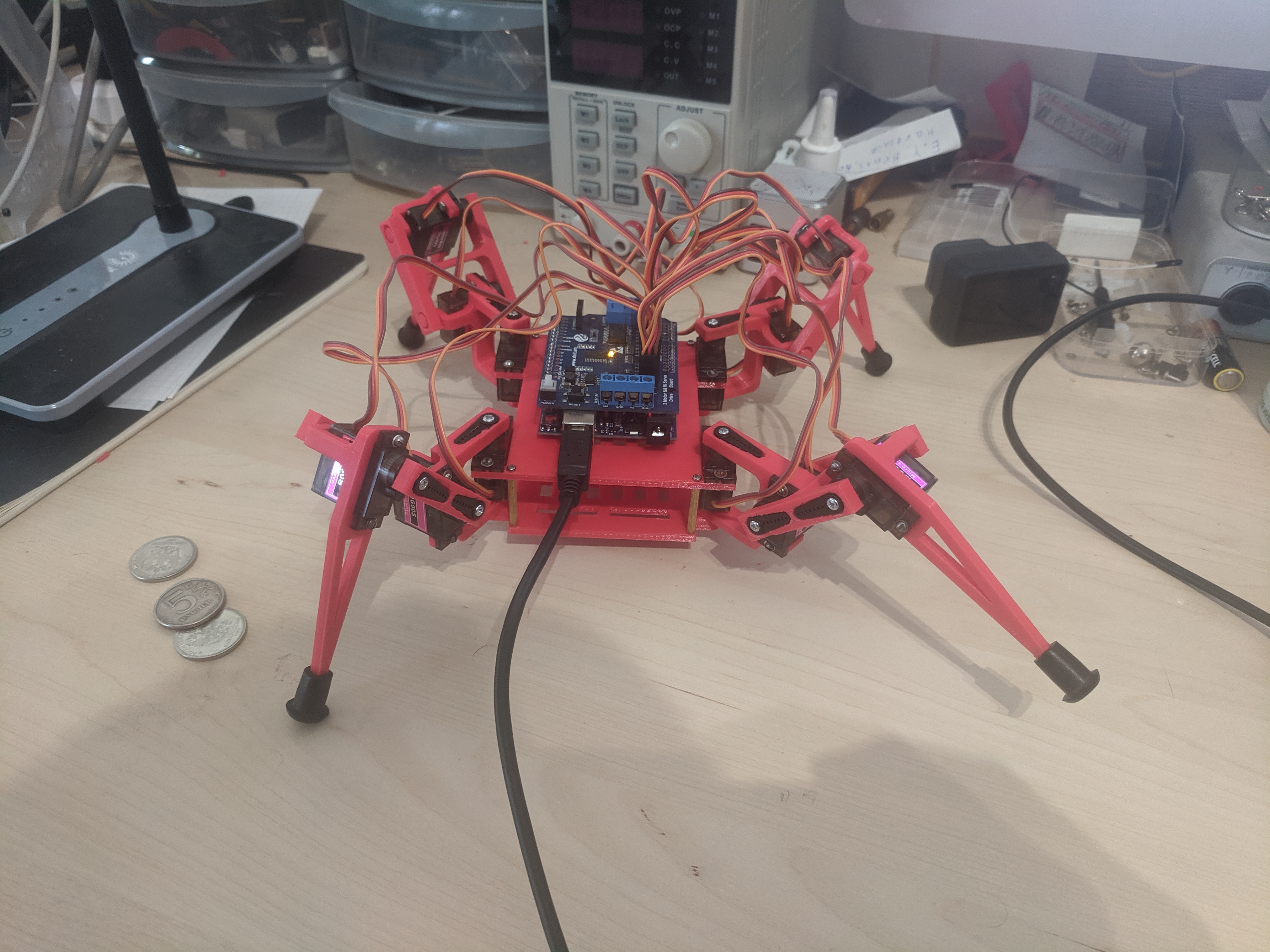
At this point I start to believe I’ll need to write a library with some geometry calculations in it. Doesn’t come as easy as I imagined starting this project. LOL.
This is the second generation of Quadropod. Features:
Replaced logic board. Moved from ESP32 to Arduino UNO + Servo Shield (16 servo, 2 DC motors). Although nice, ESP32 was giving me headaches with generated PWM for servo. Sometimes the signal was interrupted, giving wrong position to a servo. Plastic gears didn’t like that at all. 3 servos went out of order.
Upgraded motors from SG90 with plastic gears to MG90S with metal ones for more reliability and power.
Upgraded design of some plastic parts. Replaced parts that required extra assembly with solid ones.
Tips of the legs can now be augmented with rubber pads for more control on slippery surfaces.
Printing and assembling…